Understanding Feed Rollers in Woodworking Machines
Feed rollers are an integral component of woodworking machines, playing a crucial role in the overall functionality and efficiency of the equipment. These rollers are designed to grip and advance the workpiece through the machine, ensuring a steady and controlled feed. By exerting pressure on the material being processed, feed rollers facilitate smooth and precise movement, allowing for consistent and accurate cuts or shaping. Whether it’s a table saw, planer, or jointer, the reliability and performance of feed rollers directly impact the quality of work produced by woodworking machines.
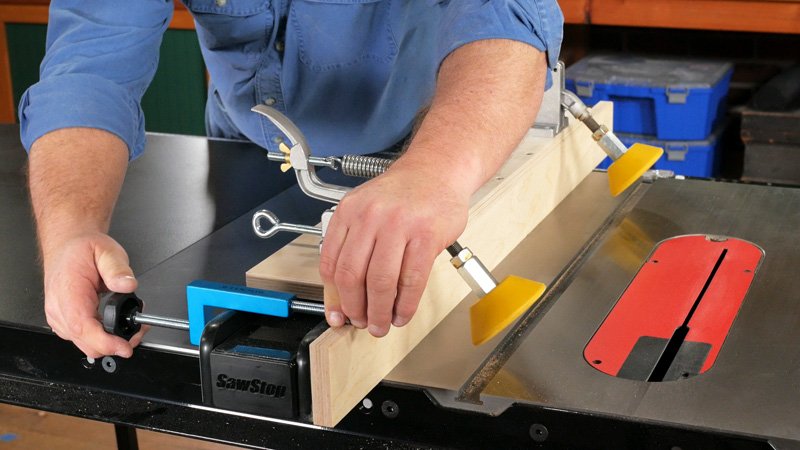
In woodworking machines, feed rollers are typically made of durable materials such as rubber or polyurethane. This ensures a firm grip on the workpiece while minimizing the risk of damage or slippage during operation. The design and texture of the feed rollers can vary depending on the specific woodworking task and the type of material being processed. The diameter and spacing of the rollers are also factors that can affect the feeding process. When properly chosen and adjusted, feed rollers provide a stable and consistent feed rate, optimizing productivity and reducing the chances of accidents or errors.
Related:-Woodworking Edge Corner Plane
Determining the Role of Feed Rollers in Woodworking Machines
Feed rollers play a crucial role in woodworking machines as they are responsible for the smooth and efficient feeding of wood materials through the machine. They provide a consistent and controlled feed rate, ensuring that the wood moves steadily and evenly, resulting in accurate cuts and precise shaping. The main purpose of feed rollers is to maintain a constant pressure on the wood, preventing any slippage or movement during the cutting or shaping process. With their strong grip, they hold the wood firmly in place, allowing the machine to perform its tasks with precision and accuracy.
One of the key functions of feed rollers is to enhance safety in woodworking machines. By securely gripping the wood, they minimize the risk of kickback, which is a sudden backward movement of the material being worked on. Kickback can be dangerous, causing injury to the operator and damage to the machine. However, with properly functioning feed rollers, the wood stays in position, ensuring a smooth and controlled feed, thus reducing the chances of kickback. Additionally, feed rollers help in minimizing the risk of accidents by preventing the operator’s hands from getting too close to the cutting tool during the feeding process. This provides a layer of protection and ensures a safe working environment for the operator.
Exploring the Functionality of Feed Rollers in Woodworking Machines
One crucial component of woodworking machines is the feed rollers, which play a vital role in ensuring the smooth and efficient operation of the machinery. The primary function of feed rollers is to grip and advance the workpiece through the machine, allowing for precise and consistent cutting or shaping. These rollers are typically made of rubber or other high-friction materials, which provide a strong grip on the wood, preventing any slipping or movement during the machining process. This ensures that the wood is fed through the machine at a consistent speed and position, leading to accurate and quality results.
In addition to their gripping capabilities, feed rollers also help to control and regulate the feed rate of the workpiece. By adjusting the pressure or speed of the rollers, operators can manage how quickly or slowly the wood is fed into the machine. This ability to control the feed rate is essential when working with different types of wood or when precision and accuracy are paramount. The feed rollers allow operators to achieve the desired outcome by controlling the pace at which the wood progresses through the machine, ensuring that each pass is uniform and consistent. This functionality of the feed rollers greatly enhances the overall performance and efficiency of woodworking machines, enabling craftsmen to produce high-quality and precise woodwork.
Important Considerations for Feed Rollers in Woodworking Machines
Feed rollers play a vital role in ensuring smooth and efficient operation of woodworking machines. When considering feed rollers for your woodworking machine, it is crucial to take certain factors into consideration. Firstly, the material of the feed roller is important. Choosing a high-quality material such as durable rubber or polyurethane can significantly impact the performance and longevity of the rollers. Additionally, the hardness and surface finish of the feed rollers are important factors to consider. Harder rollers are generally more suitable for heavy-duty applications, while smoother surface finishes can help to minimize friction and improve material feed.
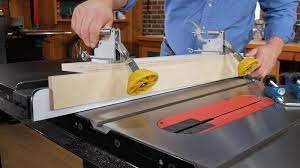
Another important consideration for feed rollers is the diameter and width. The diameter of the rollers determines the amount of contact area with the material being fed. A larger diameter usually provides better traction and grip on the material, ensuring a smoother and more consistent feed. Furthermore, the width of the rollers should match the width of the material being fed to avoid misalignment or slipping. It is important to note that the specific requirements for the diameter and width may vary depending on the type of woodworking machine and the materials being processed. Thus, consulting the manufacturer’s guidelines or seeking expert advice is recommended to ensure optimal performance.
The Importance of Proper Maintenance for Feed Rollers in Woodworking Machines
Proper maintenance is crucial for ensuring the optimal performance of feed rollers in woodworking machines. These rollers play a vital role in the feeding process by gripping and moving the material through the machine. Regular maintenance helps to prevent issues such as slippage, uneven feeding, and damage to the material.
One important aspect of maintenance is keeping the feed rollers clean. Dust, debris, and residues can accumulate on the rollers over time, leading to reduced grip and friction. Regular cleaning with a soft brush or cloth can remove these contaminants and improve the overall performance of the rollers. Additionally, it is important to inspect the rollers for any signs of wear or damage, such as cracks or uneven surfaces. Timely replacement of worn-out rollers is necessary to avoid compromising the quality of the feed and potentially causing damage to the machine or the material being processed.
Common Issues and Troubleshooting Tips for Feed Rollers in Woodworking Machines
Common Issues and Troubleshooting Tips for Feed Rollers in Woodworking Machines:
One common issue that woodworkers may encounter with feed rollers in woodworking machines is improper feeding or slipping. This can be caused by worn-out rollers or insufficient pressure exerted on the stock. To troubleshoot this problem, it is important to examine the condition of the feed rollers. If they are worn or damaged, they should be replaced. Additionally, adjusting the pressure or tension on the feed rollers can help ensure proper feeding and minimize slipping. It is recommended to consult the machine’s user manual or seek guidance from a professional if adjustments need to be made.
Another issue that may arise with feed rollers is poor traction or lack of grip on the stock. This can result in inconsistent feeding or even material damage. To address this problem, it is important to clean the feed rollers regularly to remove any debris, dust, or buildup that may affect their gripping ability. Additionally, inspecting the feed rollers for wear and tear and replacing them when necessary can help maintain proper traction. If the issue persists, it may be helpful to adjust the speed of the machine or switch to feed rollers with a different surface texture or material.
What are feed rollers in woodworking machines?
Feed rollers are components in woodworking machines that help in moving the workpiece through the machine during the woodworking process.
What is the role of feed rollers in woodworking machines?
The primary role of feed rollers is to provide a steady and consistent feeding of the workpiece, ensuring smooth and accurate movement through the machine.
How do feed rollers function in woodworking machines?
Feed rollers grip the workpiece and apply pressure to move it forward. They typically have a textured surface or rubberized coating to enhance grip and prevent slipping.
What should be considered when it comes to feed rollers in woodworking machines?
It is essential to consider the material, size, and condition of the feed rollers to ensure they are suitable for the specific woodworking application. Proper alignment and adjustment are also crucial.
Why is proper maintenance important for feed rollers in woodworking machines?
Regular maintenance helps prevent issues such as wear, damage, or buildup of debris on the feed rollers, ensuring optimal performance and prolonging their lifespan.
What are some common issues that can occur with feed rollers in woodworking machines?
Common issues include wear, damage, loss of grip, misalignment, and buildup of sawdust or debris on the feed rollers.
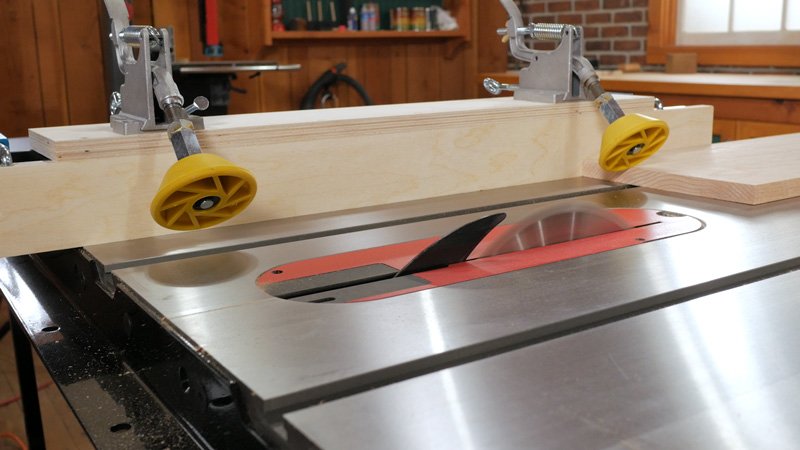
How can I troubleshoot feed roller issues in woodworking machines?
Some troubleshooting tips include cleaning the feed rollers regularly, adjusting or replacing worn-out rollers, ensuring proper alignment, and using appropriate feed roller materials for different woodworking applications.